Consumers usually care about whether the stainless steel thermos bottle is durable. The stainless steel material hardness, thickness, and bottle decoration layer adhesion fastness are the key points. This article mainly discusses how to test the spray painting layer and powder coating layer adhesion fastness on the surface of stainless steel insulated water bottles.
This article and the mentioned test standards are applicable to coatings on hard substrates (stainless steel) and soft substrates (wood and plastic) including insulated stainless steel water bottles, but these different substrates require different test procedures. This test method is also called “Cross-Cutting Test”.
The water bottle manufacturer‘s laboratory must have the full set of test equipment mentioned in this article.
1. Scope of Application
This article specifies the cross-cutting test method for evaluating the adhesion fastness of a coating layer to detachment from a stainless steel substrate when the coating is cut into a stainless steel substrate in a right-angle grid pattern. The performance measured by this empirical test procedure depends on various other factors besides the adhesion of the coating to the upper coating or substrate. Therefore, this test procedure cannot be regarded as a method for measuring adhesion.
Although this test is primarily intended for laboratory use, it is also applicable to field tests.
2. Test Equipment
2.1 Cutting Tool
It is especially important to ensure that the cutting knife has the prescribed shape and the blade is in good condition. Some suitable cutting tools are listed below, as shown in Figure 1a) and Figure 1b):
- a) The cutting edge of a single-edged cutting tool is 20 – 30 degree, and other sizes are specified in Figure 1a).
- b) Multi-edged cutting tools with six cutting blades or eleven cutting blades. The spacing between blades is 1mm or 2mm, as specified in Figure 1b).
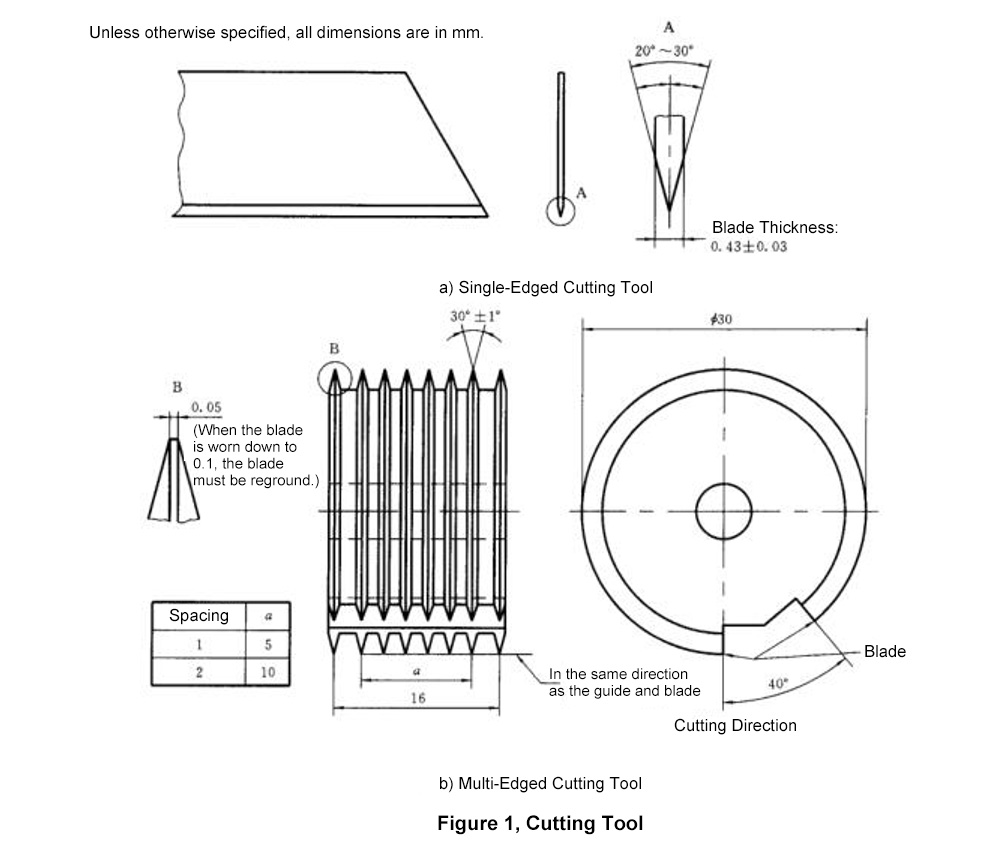
In all cases, single-edged cutting tools are the tool of choice, that is, suitable for various coatings on hard or soft substrates.
Multi-edged tools are not suitable for thick coatings (> 120 μm) or hard coatings, or coatings applied to soft substrates.
The cross-cut test of stainless steel insulation cup coating can use single-edged or multi-edged tools.
The cutting tool needs to be suitable for manual operation, although this is the more common method. The cutter can also be mounted on a motor-driven instrument for more uniform cutting. The operating procedure of the application instrument shall be mutually agreed between the purchaser and the vacuum stainless steel water bottle manufacturer.
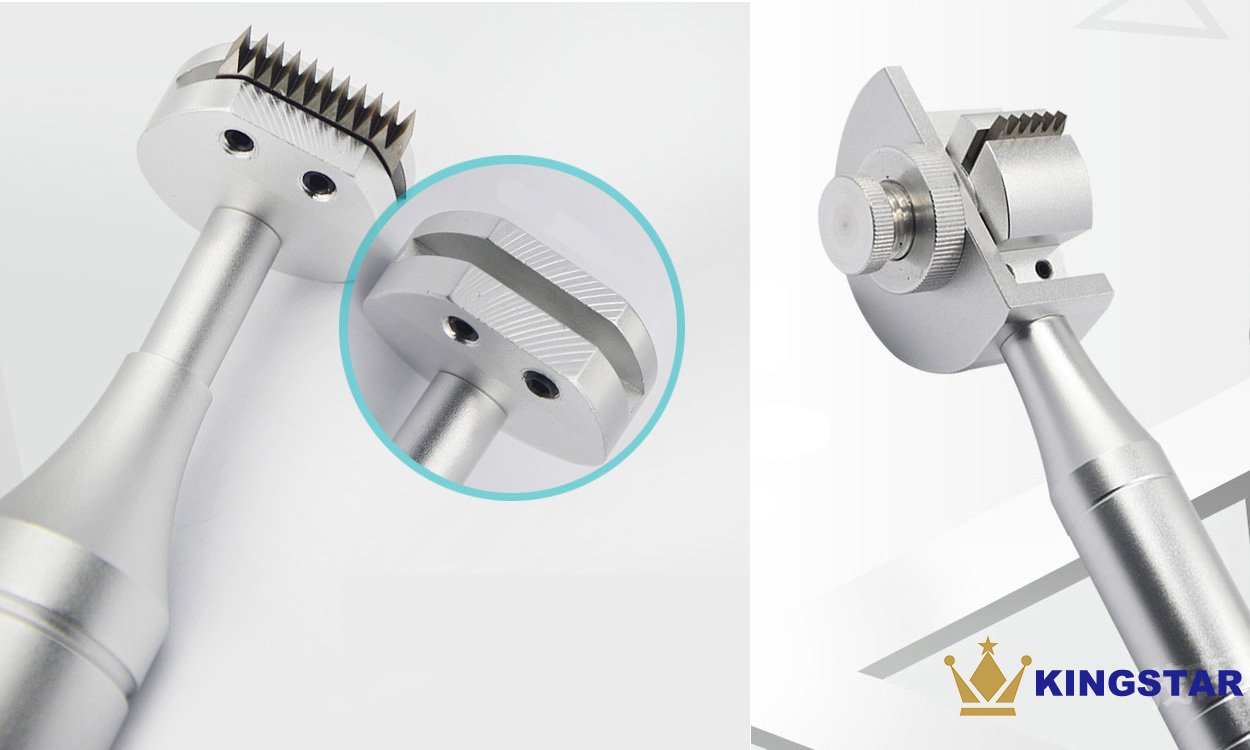
2.2 Guides and Blade Spacers
In order to cut the interval correctly, when using a single-edged cutting tool, a series of guides and blade spacing devices are required. A suitable device is shown in the figure below.
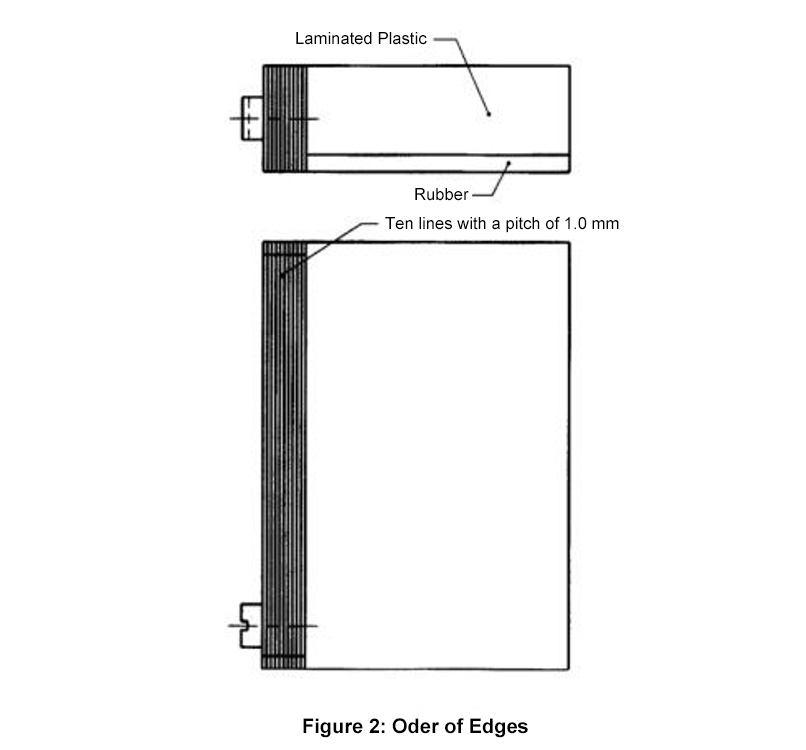
2.3 Soft Brush
2.4 Transparent Pressure-Sensitive Adhesive Tape
Adhesive tape, 25mm wide, adhesive force (10 ± 1) N / 25mm or other agreed tapes. We recommend using 3M brand Scotch 600 tape.
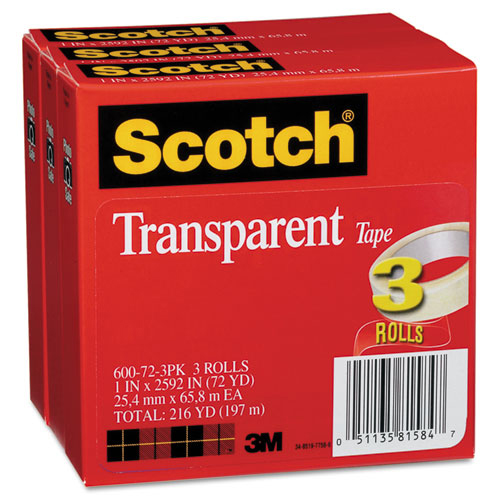
2.5 Visual Magnifier
Hand-held magnifying glass. The magnification is 2 or 3 times.
3. Sampling
According to the regulations of MIL-STD-105E, the stainless steel insulation bottle samples to be tested are randomly selected.
4. Testing Steps
Test Conditions and Testing Time
Test at least three different locations. If the three results are inconsistent, and the difference is more than one unit level, repeat the above test at three or more different positions. If necessary, test another insulated water bottle and write down all the test results.
Cut Number
The number of cuts in each direction of the cut pattern should be 6 or 11.
Cutting Spacing
The spacing of the cuts in each direction should be equal, and the spacing of the cuts depends on the thickness of the coating layer and the type of stainless steel substrate, as described below:
0 ~ 60μm: hard substrate, 1mm spacing.
0 ~ 60μm: soft substrate, 2mm spacing.
61 ~ 120μm: Hard or soft substrate, 2mm spacing.
121 ~ 250μm: Hard or soft substrate, 3mm spacing.
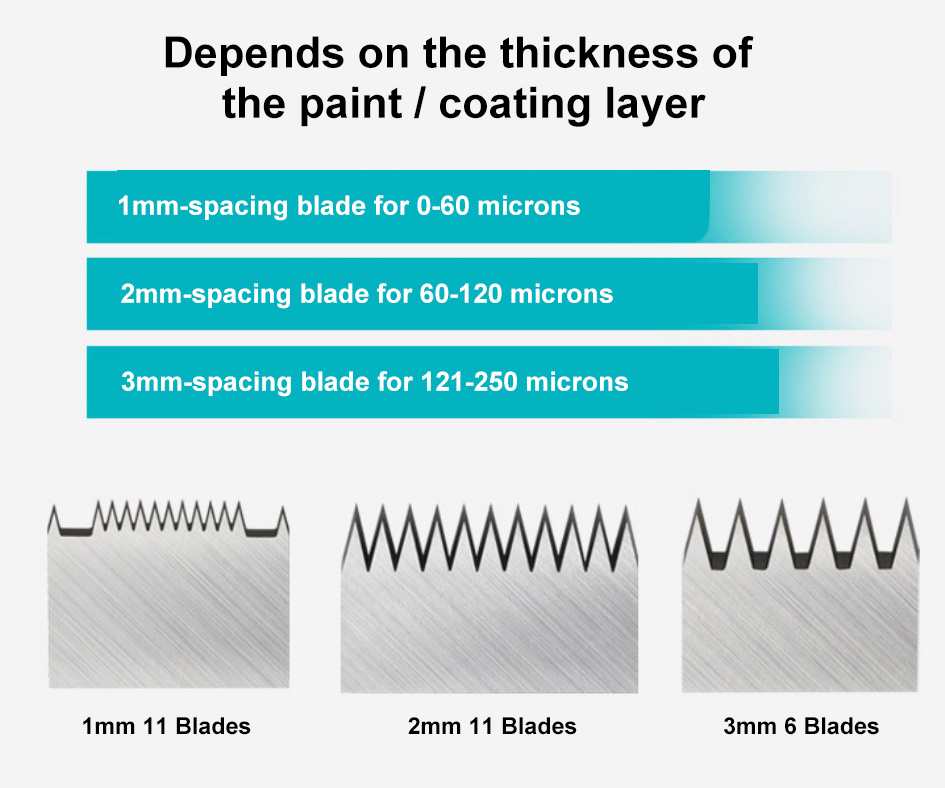
Cutting the Coating Layer by Hand
- Place the insulated stainless steel bottle on a hard, flat surface to prevent any deformation of the mug during the test.
- Perform manual cutting according to the procedure specified below.
- Before the test, check the cutting edge of the tool and keep it in good condition by sharpening or replacing with a new blade.
- Hold the cutting blade so that the blade exerts uniform force on the cutting blade perpendicular to the surface of the stainless steel water bottle, and adopts a suitable spacing guide device to form a prescribed number of cuts on the coating with a uniform cutting rate. All cuts should be made to the stainless steel surface of the substrate. If it is not possible to cut through to the substrate stainless steel due to the coating being too hard, then the test is invalid and recorded truthfully.
- Repeat the above operation, and then make the same number of parallel cutting lines and intersect the original cutting lines at a 90-degree angle to form a grid pattern.
- Use a soft-bristled brush to gently sweep back several times along the diagonal of the grid pattern, and then forward several times.
- Only hard substrates have additional adhesive tape applied. Pull out a piece of adhesive tape at a uniform speed, remove the foremost piece, and then cut out about 75 mm of adhesive tape.
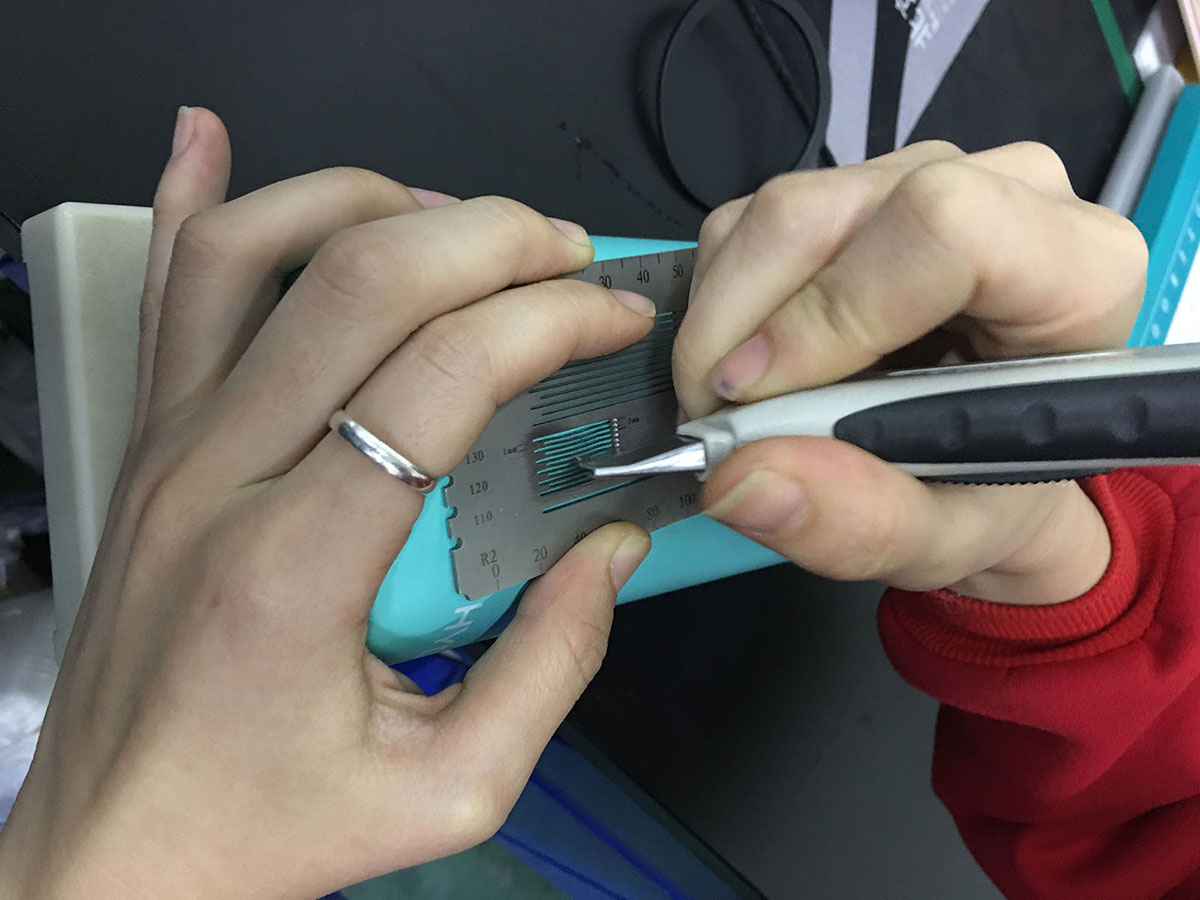
Place the center point of the adhesive tape above the grid in a direction parallel to a set of cutting lines, as shown in the figure below. Then use your fingers to flatten the adhesive tape over the grid area. The length of the adhesive tape should be at least 20mm longer than the grid.
To ensure that the adhesive tape is in good contact with the coating, use your fingertips to press the adhesive tape firmly. The full contact of the coating color seen through the adhesive tape is an effective indication.
Within 5 minutes of sticking the adhesive tape, hold the floating end of the adhesive tape, and tear off the tape smoothly within 0.5-1.0 seconds at an angle as close to 60 as possible. See the figure below.
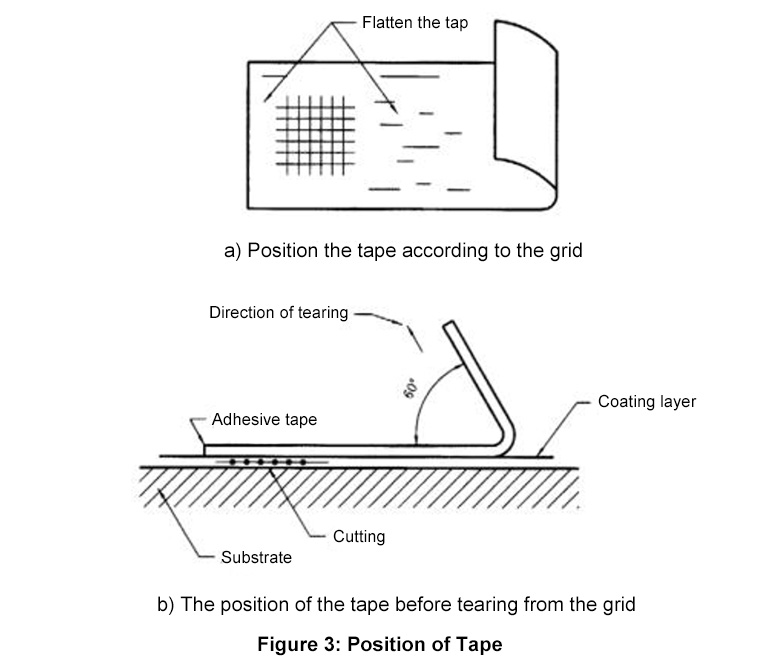
Fix the adhesive tape on the transparent film surface and keep it for reference.
5. Classification of Test Results
After the tape was removed, the results were evaluated as described below.
In a good lighting environment, use normal or corrected vision to carefully inspect the cutting area of the test coating with a visual magnifier. During the observation process, turn the stainless steel water bottle so that the observation and illumination of the test surface is not limited to one direction. It is also effective to check the adhesive tape in a similar manner.
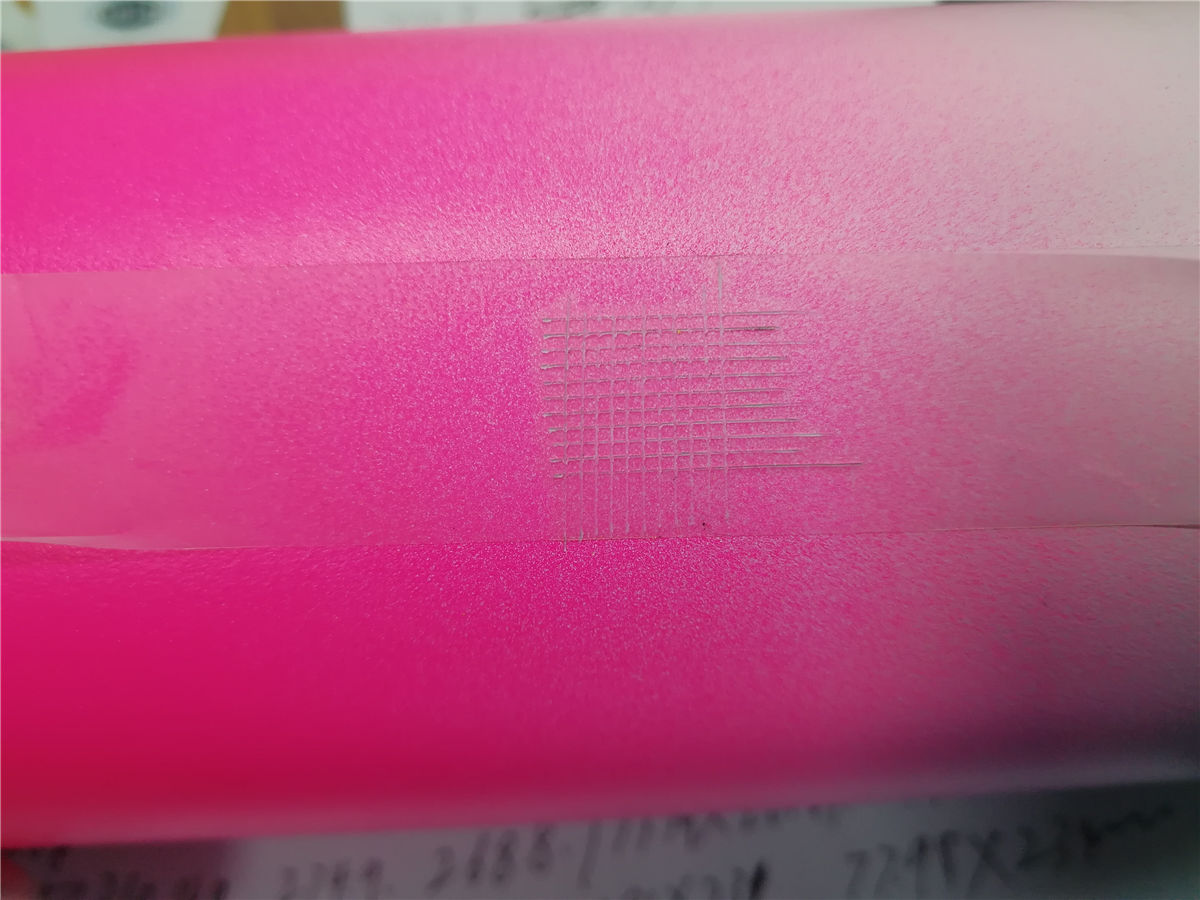
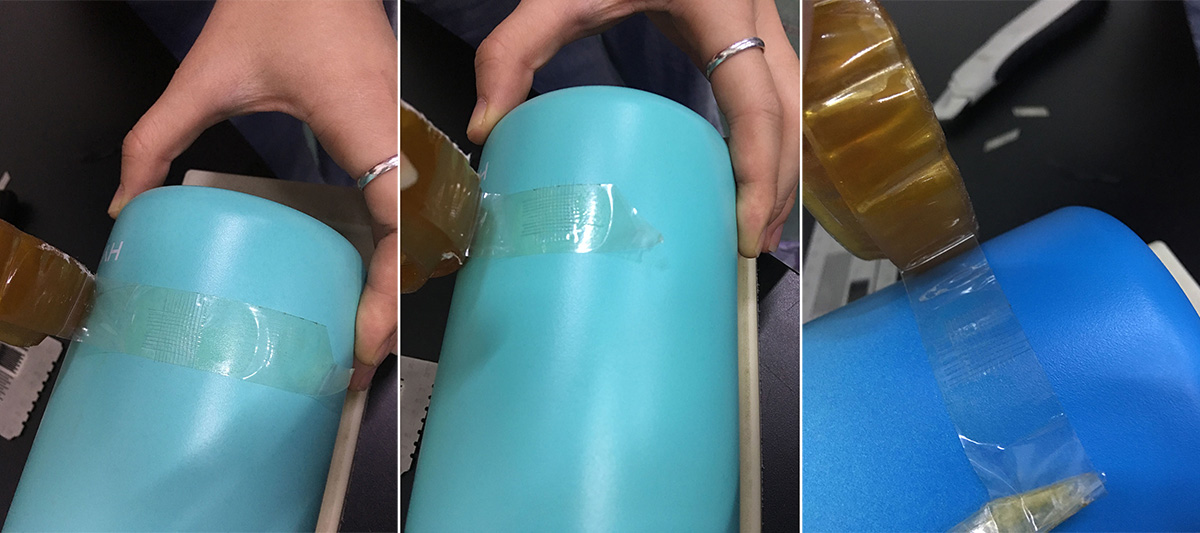
The test results are classified according to the following table by comparison with the figures.
The six levels of classification are given in the table below. For general use, the first three levels are satisfactory. The first three levels are also used when assessing ACCEPT / REJECT.
Classification of Test Results
Classification /Level |
Description of Test Result |
---|---|
0 | The cutting edge is completely smooth, without any cells falling off |
1 | There is a little coating peeling at the cross cut, but the area cannot be significantly larger than 5% |
2 | The coating is peeled off at the intersection of the incision and / or along the edge of the incision. The affected cross-cut area is obviously greater than 5%, but not significantly greater than 15%. |
3 | The coating partly or completely fell off along the cutting edge with large fragments, and / or was partially or completely peeled off at different parts of the lattice. The affected cross-cutting area was significantly larger than 15%, but not significantly larger than 35%. |
4 | The coating chipped off along the cutting edge, and / or some of the squares fell off partially or completely. The affected cross-cutting area was significantly larger than 35%, but not significantly higher than 65%. |
5 | Exfoliation is more than level 4. |
–
Here is the specific illustration
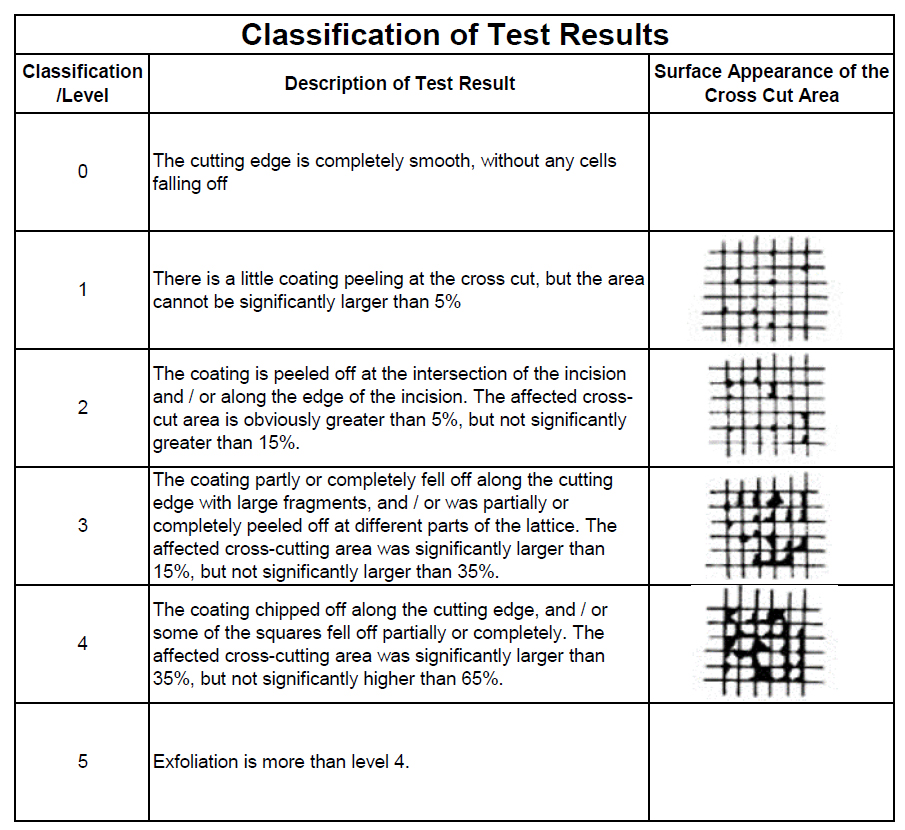
For multi-layer coating systems, any peeling that occurs between layers needs to be recorded.
If the test results are different, report each test result. In the case of a multi-layer coating system, it is necessary to record / report whether the part that has fallen off is between the coating layers or between the coating layer and the substrate stainless steel.
6. Test Report
The test report should include at least the following:
- Identify all necessary details required for the thermos cup under test;
- Indicate reference to this standard;
- The type of cutting tool used;
- Any differences from the specified test methods;
- Test date.