1. Scope
This standard specifies the terms and definitions, product classification, requirements, test methods, inspection rules, signs, packaging, transportation, and storage of vacuum sealed stainless steel bottles, cups, mugs, tumblers in bulk, jugs, carafes, growlers, pints, glasses, food jars, bowls, pots, salad bowls, and other drinkware, containers, vessels. (Hereinafter referred to as “product”)
This standard applies to stainless steel vacuum cups, bottles, pots and other daily utensils (hereinafter referred to as “products”) that store liquids such as cold and hot water and beverages.
2. References
Hygienic Standards For Rubber Products For Food
Analysis Method Of Hygienic Standard Of Rubber Gasket (Ring) For Food
Analysis Method Of Hygienic Standard Of Stainless Steel Food Container
Sanitary Standards For Stainless Steel Tableware Containers
Sampling Inspection Procedure. Part 1: Batch inspection sampling plan retrieved by acceptance quality limit (AQL)
3. Products, Parts, and Parameter
3.1 Vacuum insulated stainless steel flasks, bottles, pots and other containers.
The product is one kind of household appliances mainly made of stainless steel and used to store liquids such as cold and hot water, beverages, The has the function of whose function is for heat preservation (or cold preservation)
3.2 Main body
The vacuum part is composed of inner shell and outer shell.
3.3 Inner shell
The inner part of the main body which is in touching with the beverages directly.
3.4 Outer shell
The outer part of the main body which connect to the inner shell.
3.5 Lower stopper
Lower stopper, separated from the product cover, it is used to seal the mouth of the appliance, and has the function of water resistance (control) and heat preservation.
3.6 Calibre, Minimum diameter
Minimum inner diameter of the mouth of the inner shell (please refer to Appendix A)
3.7 Capacity
The actual volume of full with water after being sealed by the original cap (plug)
3.8 Nominal capacity, Marked capacity
The capacity stated on the product or packaging.
4. Product Category
4.1 Products are divided into stainless steel vacuum cups, bottles, and pots according to their shapes and functions (please refer to Appendix A)
4.2 According to the sealing form, the products are divided into: with inner plug and without inner plug.
4.3 Product specifications are expressed in liters or milliliters (L/ml) of marked capacity in Chin and Japan and some Asia countries. In Europe and the U.S, it is OZ and LB.
5. Requirements
5.1 Material
5.1.1 General requirements
Under the foreseeable use conditions, the selected materials of the product should not release any substances that may be harmful to health or components that have adverse effects on any organic tissues.
5.1.2 Material and hygiene requirements of main parts
5.1.2.1 The product inner shell should be made of 12Cr18Ni9 (equivalent to SS302) and 06Cr19Ni10 (equivalent to SUS304, 18/8) stainless steel materials specified in GB/T3280. Hygiene requirements should meet the requirements of the GB 9684 standard.
5.1.2.2 The outer shell of the product should be made of austenitic stainless steel and meet the physical and chemical indexes specified in Table
Table 1 Physical and chemical indexes of austenitic stainless steel
Components | Standards |
Pb. mg/L in 4% acetic acid soaking solution≤ | 1.0 |
Cr. mg/L in 4% acetic acid soaking solution≤ | 0.5 |
Ni, mg/L in 4% acetic acid soaking solution≤ | 3.0 |
Cd, mg/L in 4% acetic acid soaking solution≤ | 0.02 |
As, mg/L in 4% acetic acid soaking solution≤ | 0.04 |
Note: The soaking conditions are all boiling for 30 minutes, and then test at room temperature for 24 hours. |
5.1.3 Accessories’ materials and hygiene requirements
5.1.3.1 All metal accessories that are in direct contact with liquids should be made of 12Cr18Ni9 (equivalent to SS302) and 06Cr19Ni10 (equivalent to SUS304, 18/8) stainless steel materials specified in GB/T3280.
5.1.3.2 The silicone parts used in the product should meet the requirements of GB4806.1.
5.1.3.3 The plastic parts used in the product should meet the requirements of national health standards.
5.1.3.4 The hygienic requirements for the surface coating of the product shall comply with the provisions of 4.3 in GB 6675.
5.2 Capacity
The product capacity deviation is allowed to be within ±5% of the nominal capacity.
5.3 Insulation performance
5.3.1 The thermal insulation performance of products with inner plugs shall not be lower than those specified in Table 2.
Table 2 Thermal insulation performance of products with plug
Unit:℃
Capacity
(L) |
Diameter(mm) | |||||
<34 | ≥34~<39 | ≥39~<44 | ≥44~<54 | ≥54~<74 | ≥74 | |
<0.3 | ≥35 | ≥33 | ≥31 | ≥28 | — | — |
≥0.3-<0.4 | ≥40 | ≥38 | ≥36 | ≥33 | ≥30 | ≥28 |
≥0.4-<0.6 | ≥45 | ≥43 | ≥41 | ≥37 | ≥34 | ≥32 |
≥0.6-<0.9 | ≥50 | ≥48 | ≥44 | ≥41 | ≥38 | ≥34 |
≥0.9-<1.2 | ≥56 | ≥53 | ≥50 | ≥47 | ≥44 | ≥40 |
≥1.2-<1.5 | ≥61 | ≥58 | ≥55 | ≥52 | ≥49 | ≥45 |
≥1.5-<1.8 | ≥64 | ≥61 | ≥58 | ≥55 | ≥52 | ≥48 |
≥1.8 | ≥65 | ≥63 | ≥61 | ≥58 | ≥55 | ≥51 |
Note: The temperature measurement time for products with inner plugs is 24 hours. |
5.3.2 The thermal insulation performance of products without inner plugs shall not be lower than those specified in Table 3.
Table 3 Thermal insulation performance of products without plug
Unit: ℃
Capacity
(L) |
Diameter (mm) | |||||
<34 | ≥34~<54 | ≥54~<74 | ≥74~<94 | ≥94~<110 | ≥110~<125 | |
<0.4 | ≥42 | ≥40 | ≥38 | ≥35 | ≥33 | ≥31 |
≥0.4~<0.6 | ≥44 | ≥42 | ≥40 | ≥39 | ≥35 | ≥33 |
≥0.6~<0.9 | ≥48 | ≥46 | ≥44 | ≥41 | ≥38 | ≥36 |
≥0.9~<1.2 | ≥54 | ≥52 | ≥49 | ≥46 | ≥42 | ≥40 |
≥1.2~<1.5 | ≥56 | ≥54 | ≥52 | ≥50 | ≥48 | ≥45 |
≥1.5~<1.8 | ≥57 | ≥56 | ≥55 | ≥53 | ≥50 | ≥47 |
≥1.8 | ≥58 | ≥57 | ≥56 | ≥55 | ≥53 | ≥50 |
Note: The temperature measurement time of products without inner plug is 6 hours. |
5.3.3 The heat preservation efficiency shall meet the requirements of Table 2 and Table 3 respectively after tested according to testing 6.4
5.4 Impact resistance
The product should be free of defects such as water leakage, cracks and breakage that affect its use, and the insulation performance should still meet the requirements of Table 2 and Table 3 after tested according to testing 6.5
Note: There is no water leakage requirement for products sealed with non-threaded screw structure.
5.5 Sealing cover (plug) and hot water smell
The cover (plug) and hot water should have no obvious peculiar smell after tested according to testing 6.6
5.6 Hot water resistance of silicone parts
It should not be sticky, and the appearance should have no obvious deformation after tested according to 6.7
5.7 Handle and loops assembling strength
There should be no damage after tested according to 6.8
5.8 Strap strength
The straps and its joints shall not slip or break after the tested according to 6.9
5.9 Color fastness of strap
After the test according to 6.10, the color fastness of the strap should meet the requirements of level 3 or higher specified in GB 251.
5.10 Sealing performance
The hot water should not leak out after the sealing parts tested according to 6.1
5.11 Coating adhesion
The coating shall retain more than 92 checkerboards after tested according to 6.12
5.12 Adhesion of the prints on the coated surface
The prints shall not fall off after tested according to 6.13
5.13 Screwing strength of sealing cover (plug)
The product cover (plug) should not slip after testing according to 6.14
5.14 Performance
The movable parts are installed firmly and flexible, and the function is normal
5.15 The surface appearance
5.15.1 The outer surface of the product has uniform color, no cracks or gaps are allowed, and the welding place should be smooth and free of burrs.
5.15.2 The inner surface of the product should be smooth and uniform, without obvious scratches, pits and deformation.
5.15.3 All parts have uniform color, no burrs on the surface, no obvious scratches
5.15.4 The prints should be clear and completed
5.15.5 Electroplated parts should not be exposed, peeled or rusted
5.15.6 The product mark should be correct, clear and complete, and comply with 8.1.1 mark requirements
advanced water bottle production line
6. Test Methods
6.1 Test conditions
6.1.1 Test equipment includes
- a) Two hard wood boards withspecification of 900×600×30mm
b)One bracket for impact test
- c) One set of reflux condenser;
d)One torque machine:0-100kgf·cm
e)One digital thermometer with an accuracy of 0.1℃;
f)A thermocouple thermometer with an accuracy of 1.5℃
g)An electronic scale with an accuracy of 1g
h)Adhesive force of glass tape 10±1N/25mm
i) Vernier calipers, circle rulers, stopwatches, weights, knives, scissors, lanyards, fitter tools etc.
6.2 The chemical composition of metal material stainless steel shall be inspected according to GB/T223 steel product analysis method.
6.3 Capacity test
a)Put the empty product with cover (plug) on the weighing instrument and call the mass G1
b)Fill the product with water at room temperature, seal it with the original cap (plug), and call its quality G2.
c)Calculate its volume V according to formula (1)
V = (G2-G1) / ρ……………………………………(1)
In the formula(1): G1-product mass; unit is kilogram (Kg)
G2—The quality of the product with water; the unit is kilogram (Kg)
V—Volume; unit is liter (L)
ρ—The density of water, take 1 Kg/L
6.4 Thermal insulation performance test
Keep the product opening at the specified ambient temperature (20℃±5℃) for more than 30 minutes, and fill it with boiling water to the lower end of the sealing cap (plug). When the measured temperature in the product reaches 95℃±1℃, immediately tighten the seal. Under the same environmental conditions, after 24 h or 6 h, determine the internal water temperature of the product.
6.5 Impact resistance test
Including drop impact test and swing impact test, according to Appendix B test method.
6.6 Sealing cover (plug) and hot water smell
After cleaning the product with warm water at 40℃~60℃, fill it with hot water above 90℃, tighten the cap (plug) and leave it for 30 minutes, then check the cap (plug) and hot water respectively.
In case of dispute, the same judgment of at least three of the five inspectors shall prevail.
6.7 Hot water resistance test of silicone parts
Follow the test method in Appendix C.
6.8 Handle and loops assembling strength
Follow the test method in Appendix D.
6.9 Strap strength
Follow the test method in Appendix E.
6.10 Color fastness of strap
Test according to GB/T3922 method.
6.11 Sealing performance test
Fill the product with 50% capacity of hot water above 90°C. After sealing, the mouth is upward, and the product is waved up and down 10 times at a frequency of 1 time/S and an amplitude of 500 mm to check for water leakage.
Note: This test is not done for products sealed with non-threaded screw structure
6.12 Coating adhesion test
Use a cutting tool to mark 100 (10×10) 1mm2 grids with a depth of 1mm2 on the printed coating surface of the test piece at an angle of 30°, and glue them with a width of 25mm and an adhesive force of (10±1) N/ 25mm tape, then peel off the tape in a direction at right angles to the surface, and count the number of remaining grids that are not peeled off. off.
6.13 The surface prints adhesion test
On the text and pattern, stick a tape with a width of 25mm and an adhesive force of (10±1) N/25mm, and then peel off the tape in a direction at right angles to the surface to check whether it has fallen off.
6.14 Screwing strength test of sealing cap (plug)
For products that use threaded seals, first tighten the cover (plug) by hand, and then apply a torque of 3Nm to the cover (plug) to check for sliding teeth.
6.15 Hygiene requirements test
- a) The hygienic requirements of stainless steel materials are tested in accordance with GB/T 5009.81.
- b) The hygienic requirements of silicone parts are tested in accordance with GB/T 5009.64.
- c) The hygienic requirements of plastic parts are tested in accordance with GB/T 5009.60.
- d) The hygienic requirements of the coating are tested in accordance with Appendix C of GB 6675.
6.16 Appearance inspection
Test with touching feel and visual inspection
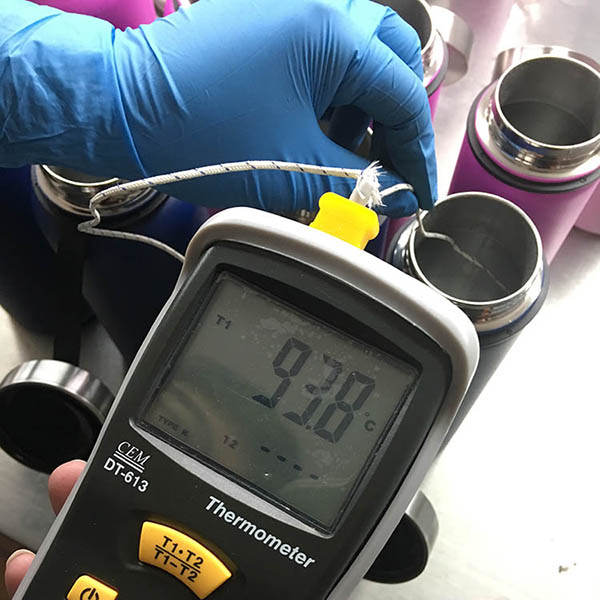
insulation performance testing
7. Testing Regulations
7.1 Product inspection is divided into factory inspection and type inspection.
7.2 The factory inspection items, inspection level, unqualified classification and acceptance quality limit (AQL) comply with the requirements of Table 4.
Table 4 Factory inspection items and judgment
No. | Test Items | Unqualified Classification | Corresponding Clause | Check Level | Acceptance Quality Limit(AQL) |
1 | Insulation performance test | A | 5.3 | S-2 | 4.0 |
2 | Sealing cover (plug) screwing strength test | 5.13 | |||
3 | Sealing performance test | 5.10 | |||
4 | Seal cover (plug) and hot water smell test | B | 5.5 | S-2 | 6.5 |
5 | Coating adhesion test | 5.11 | |||
6 | Prints adhesion test | 5.12 | |||
7 | Performance test | 5.14 | |||
8 | Appearance test | C | 5.15 | S-2 | 10 |
7.3 The one-time sampling plan of Level II is calculated based on the number of unqualified products per 100 units.
7.3.1 Type inspection should be carried out when the product is in one of the following situations
a)New product or old product transfer to factory production trial formulation appraisal
b)After formal production, if there are major changes in structure, materials, and processes, which may affect product performance
c)During normal production, type inspection shall be carried out every year annually
d)When the product has been discontinued for more than six months and resumed production
e)When there is a big difference between the factory inspection result and the last type inspection
f)When the national quality supervision agency puts forward a requirement for type inspection.
7.3.2 Inspection items, unqualified classification, discrimination level, container sample size, unqualified quality level (RQL)
Refer to Table 5.
Table 5 Type inspection items and inspection standard
No. | Items | Unqualified Classification | Corresponding Clause | Inspection Standard | Container Sample size | Unqualified Quality Level(RQL) |
1 | Hygiene requirements test | A | 5.1.2、5.1.3、 | Ⅱ | n=3 | 50 |
2 | Impact resistance test | B | 5.4 | Ⅱ | n1=n2=3 | 65 |
3 | Hot water resistance of silicone parts test | 5.6 | ||||
4 | Handle and loops assembling strength test | 5.7 | ||||
5 | Strap strength test | 5.8 | ||||
6 | Capacity test | 5.2 | ||||
7 | Insulation performance test | 5.3 | ||||
8 | Seal cover (plug) and hot water smell test | 5.5 | ||||
9 | Sealing performance test | 5.10 | ||||
10 | Sealing cover (plug) screwing strength test | C | 5.13 | Ⅱ | n1=n2=3 | 80 |
8. Marking, Packaging, Transportation and Storage
8.1 Marking
8.1.1 There should be a clear and permanent mark on the obvious position of the product
a) Manufacturer name or trademark
8.1.2 The packaging box should have the following signs
a) Trademark
b) Product name and specifications;
c) Main product material and heat preservation efficiency;
d) Implementation standard number and name;
e) Company name, factory address, contact number and postal code
- 1. 3The storage and transportation pictorial signs on the packing box should comply with the relevant regulations of GB/T 191, and the receiving and shipping signs should comply with GB/T 6388
The relevant regulations of, and should have the following signs
a) Trademark
b) Product name and specifications;
c) Implementation standard number and name
d) Company name, factory address, contact number and postal code
e) EXW year and month
f) Quantity
g) Net weight, gross weight, measurement(L*W*H)
h) Aware of getting wet, upwards, handle the signs carefully
8.2 Certificate of conformity
The product certificate should have the following contents:
a) Trademark
b) Qualification certificate (inscription) and inspector (signature or code)
c) Manufacture date
d) Water bottle manufacturer name
8.3 Instruction manual
The instruction manual should include the following:
a) Please read the instruction manual carefully
before use:
b) Stainless steel material grade of the product body Save
c) Instructions for use;
d) Precautions
- Be careful not to store carbonated beverages (unless the manufacturer expresses it)
- Not to be used to keep dairy products or baby food (risk of bacterial growth
- Do not use heating equipment such as microwave ovens to heat or heat the product;
- Do not use dishwasher unless the manufacturer specify it
e) Product implementation standard number and name
f) Company name, factory address, contact number and postal code
8.4 Packaging, transportation and storage
8.4.1 Package
8.4.1.1 Product packaging should be dry, complete and clean, with instructions for use and certificates of conformity attached.
8.4.1.2 Products using plastic packaging should meet the requirements of the GB 4803 standard
8.4.1.3 The products packaged in corrugated cartons in accordance with the regulations of GB/T 6543
8.4.2 Transportation
8.4.2.1 During transportation, loading and unload with care, and it is strictly forbidden to throw, roll and step on
8.4.2.2 Beware of moisture, squeezing and rain during transportation
8.4.2.3 It is strictly prohibited to ship with corrosive items at the same time
8.4.3 Storage
8.4.3.1 The product should be stored in a ventilated, non-corrosive material and gas, and the relative humidity should be less than 85% in a warehouse.
8.4.3.2 Keep the product storage distance above 200mm from the wall, above 100mm from the ground, and no more than 3m stack height.
This standard is only for water bottle factory, drink bottle supplier, purchaser, and consumer reference.
Appendix A
(Informative appendix)
Product Structure
A.1
The structure type and part name of the stainless steel vacuum cup are shown in Figure A.1
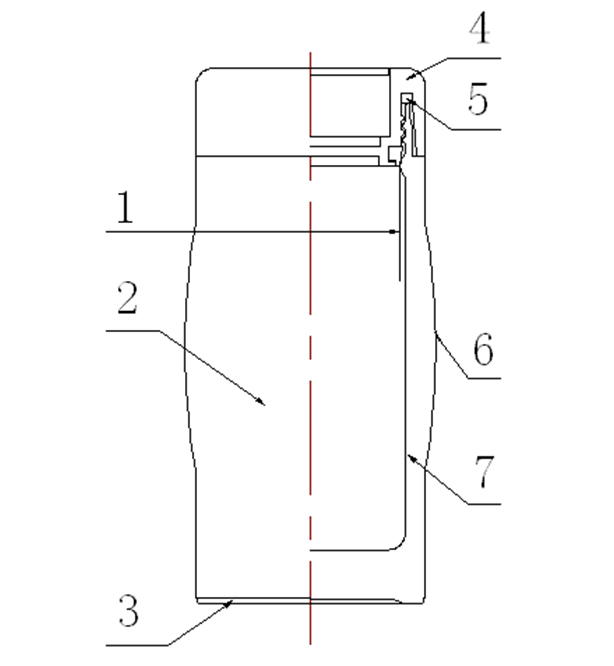
Note:
1 – Mouth Diameter 2 – Body 3 – Bottom 4 – Lid
5 – Silicone Seal 6 – Outer Shell 7 – Inner shell
Figure A.1
Schematic diagram of vacuum insulated bottle structure
A.2
The structure type and part name of the vacuum insulated stainless steel water bottle are shown in Figure A.2.
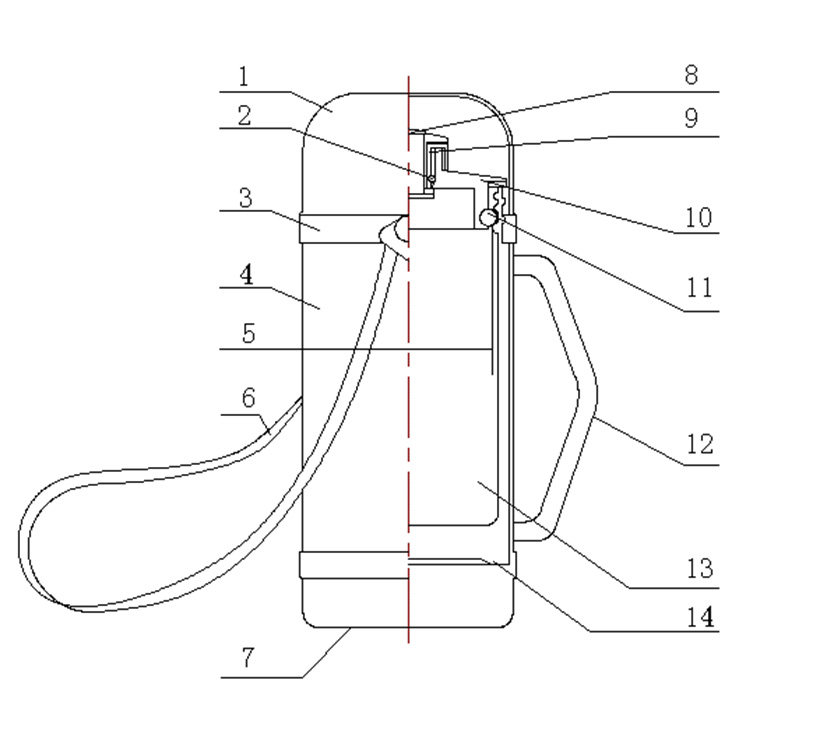
Note:
1 – Outer Cover 2 – Plug 3 – Sleeve 4 – Body 5 – Mouth Diameter 6 – Strap 7 – Bottom 8 – Outlet Valve 9 – Inner Stoper 10 – Inner Lid 11 – Silicone Seal 12 – Handle 13 – Inner Shell 14 – Outer shell
Figure A.2
Schematic diagram of vacuum bottle structure
The structure type and part name of the stainless steel vacuum pot are shown in Figure A.3
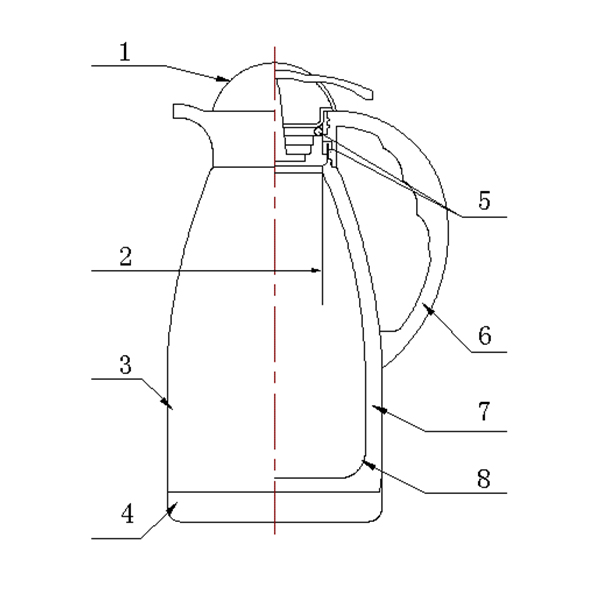
Note:
1 – Lid 2 – Mouth Diameter 3 – Body 4 – Bottom 5 – Silicone Seal
6 – Handle 7 – Outer shell 8 – Inner Shell
Figure A.3 Schematic diagram of vacuum pot structure
Appendix B
(Normative appendix)
Product impact test method
B.1 Drop test (Drop impact test)
a)Fill the product with water at room temperature (5°C~35°C) and seal it, hang it vertically at a height of 400mm with a lanyard, and drop it on a fixed horizontal hard wood board with a thickness of more than 30mm in a static state. (Figure B.1 a)
b) Fill the product with water at room temperature (5°C~35°C) and seal it, hang it horizontally at a height of 400mm with a lanyard, and drop it to a fixed horizontal hard wood board with a thickness of 30mm or more in a static state.
Unit: mm
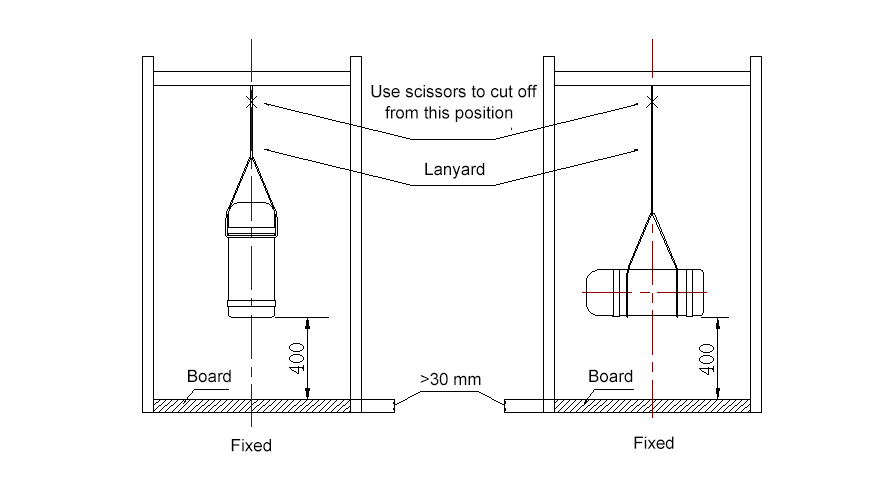
1. Vertical suspension
2. Horizontal suspension
Figure B.1: Schematic diagram of drop impact test
B.2 Swing impact test
Fill the product with water at room temperature (5°C~35°C) and seal it, fix it with a lanyard, keep it 400mm in length, lift it to a 45° angle, and hit a vertically fixed hard wood board with a thickness of 30mm or more.
Unit: mm
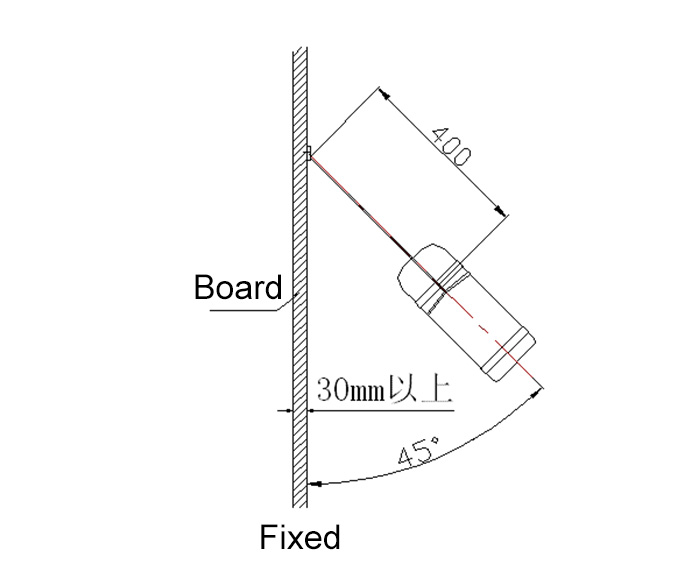
Figure B.2: Schematic diagram of swing impact test
Appendix C
(Normative appendix)
Test method for hot water resistance of silicone parts
C.1 Hot water resistance test
In addition, after placing it at normal temperature for 2 hours, check the naked eye for obvious deformation.
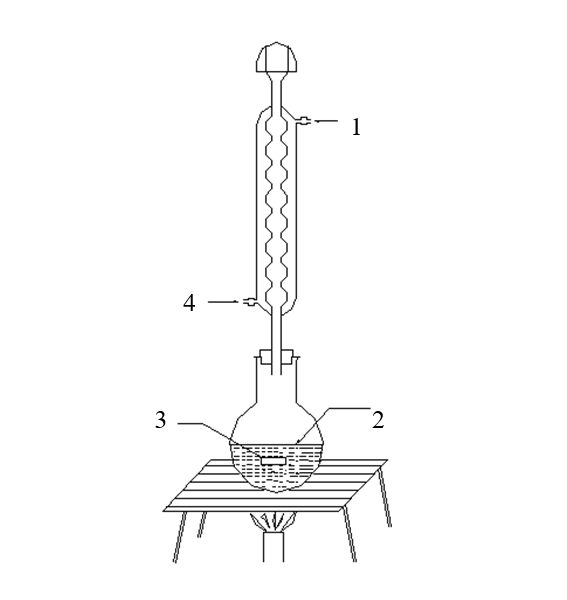
Note:
1 – Reflux Condenser 2 – Distilled Water 3 – Silicone parts 4 – Water
Figure C.1 Schematic diagram of hot water resistance test of silicone parts
Appendix D
(Normative appendix)
Test method for the assembling strength of handle and loops
D.1 Test for the assembling strength of handle and loops
Hang the product through the handle or lifting ring, and put a weight equivalent to 6 times the weight of the product full of water (including all accessories).
Hang it gently on the product as shown in Figure D.1, keep it for 5 minutes, and check the handle or lifting ring.
Unit: mm
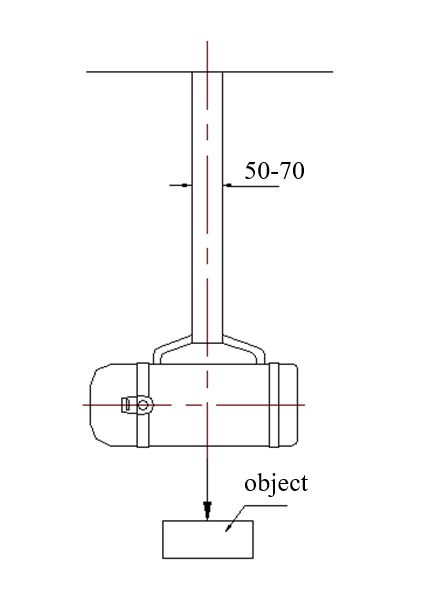
Figure D.1 Schematic diagram of assembling strength test of handle and loops
Appendix E
(Normative appendix)
Test method of strap strength
E.1 Strap strength test
Unfold the strap to the longest point, then hang the product through the strap, and fill the product with water (including all accessories)
A weight of 10 times the weight should be lightly hung on the product as shown in Figure E.1 and kept for 5 minutes. Check the strap and its connection.
Unit: mm
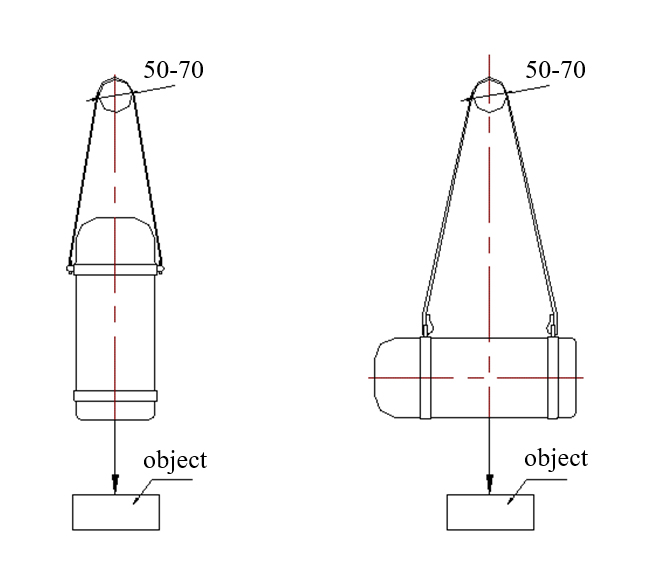
1. Vertical suspension
2. Horizontal suspension
Figure E.1 Schematic diagram of strap strength test